Core Tip: Diamond geological oil mining bit plays a huge role in oil exploration and mineral mining. All countries in the world pay attention to the research of drilling bit technology. At present, great progress has been made in diamond bit design, cutting tooth development, and hydraulic energy utilization research at home and abroad, and many new theories, new technologies and new products have been introduced.
As we all know, drilling is the "leading" of oil exploration and development. There is a famous saying in the industry: "The drill bit is not enough, the oil does not take the risk", which is the truth. This is an analogy to the important position of drilling engineering in oil and gas field exploration and development projects, and it also shows the important role of the “bit”, the hardware used for rock drilling and hole drilling. Therefore, all countries in the world are paying more attention to the research of drilling technology, and work harder to develop high-efficiency drill bits and research and development of new products.
Diamond pdc drill bit
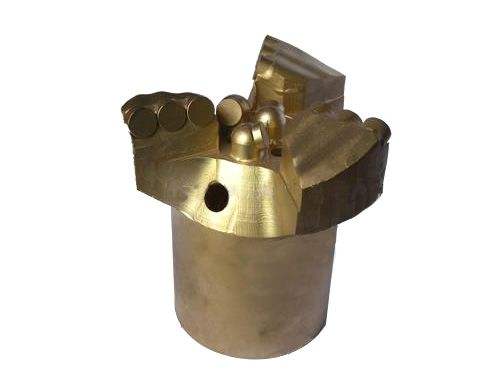
1 New technology, new technology
Some major drill design and manufacturing companies, represented by Hughes Christensen, have done a lot of work in the improvement and development of drill bits, and have achieved gratifying results. Hybrid drill bits, anti-rotation drill bits, anti-vibration drill bits, Fast hard formation drills, double-cutting structural drills, new diamond drills, etc. The latest research results are:
1.1 On the basis of stress-treated teeth, black ice polishing teeth and hard alloy supporting edge teeth, a new cutting structure such as thickened composite cutting teeth and double cutting cutting teeth was developed.
1.2 In the research of diamond bit mechanics, there are also new breakthroughs, and the new hydraulic design schemes such as the diffuse hydraulic design concept (ie, a symmetric nozzle near and away from the center of the bit to make the hydraulic energy distribution more reasonable) and the special-shaped nozzle structure are proposed. .
1.3 At the same time, in recent years, the study of using the principle of electro-osmosis to reduce bit mud packs has been active, and the process of gas nitriding treatment has been developed to make the surface of the drill bit negatively charged.
1.4 A lot of work has been done in strengthening the diameter keeping, improving the chip flute design, extending the life of the drill bit, hardening the surface of the steel bit, increasing the cutting area, and effectively removing the cuttings, and achieved many results.
1.5 The specifications of diamond bit cutting components have also evolved from a single variety to today's variety. At present, the thermally stable polycrystalline diamond has a triangular polycrystalline series, a cylindrical series, and a ceramic series; the polycrystalline diamond composite has a diameter of 3/8", 1/2", 3/4", 1" series, etc., from the conventional film. To the claw piece, the curved piece, the refining piece, etc., the variety of the cutting element is diversified.
2 new products
In recent years, foreign companies such as Christensen, Smith, Hycalog, Secu2rityDBS, and Geodiamond, as well as domestic Chuanke, Xinxing, Petroleum University (East China), Shengli Oilfield, etc. are all committed to the development and improvement of diamond drill bits, and introduced a number of innovative designs. Drill bit.
2.1 New diamond drill bit for multiple formations
A drill called "transformation" drills a soft formation as fast as a bit with a low density of teeth, and when drilled in a harder formation, it is as durable as a drill with a high density of teeth. Sex. This feature is achieved by combining the variable angle characteristics between the main and auxiliary blades with a patented new hydraulic system. This type of drill is equipped with two types of scrapers, and the drill can be applied to various formations by adjusting the cutting action of the two scrapers.
2.2 Multi-water eye diamond drill bit
Hughes Christensen recently developed a multi-water diamond drill with five scraper blades and 19mm cutting teeth. This multi-eye diamond bit is equipped with two inclined central main nozzles and eight auxiliary water eyes. The flow through the nozzle and the water eye points to each cutting tooth, increasing the total flow area from 484mm2 to 774 square mm2, reducing the pressure drop at the drill bit, achieving a larger flow rate, and consuming only 5% of the pump pressure at the drill bit. Effectively removes the bit mud pack. This design also increases the efficiency of the drill bit in the low water horsepower range.
Hughes Christensen has added tungsten carbide support edge (CSE) cutting teeth to the design of this drill bit to prevent early breakage of the cutting teeth. Later, high-quality polished black ice CSE cutting teeth were used to further improve the wear resistance and working performance of the drill. This drill is used in conjunction with Beck Hughes Inteq's bottom mud motor.
2.3 Hydraulically assisted rock breaking bit with self-sharp cutting teeth
The University of Petroleum (East China) has developed a new type of hydraulic assisted rock breaking system with self-sharp cutting teeth, which not only improves the cooling of the working cutting teeth, but also achieves the purpose of hydraulic-mechanical rock breaking. The drill bit is composed of a drill bit body, a hydraulic injection system and self-sharp cutting teeth, characterized in that the hydraulic injection system is composed of a central radial inclined nozzle and an outer ring near tangential nozzle disposed at the top of the drill base body, and The sharp cutting teeth are arranged at the top of the drill bit body. The test results show that because the drill adopts a reasonable hydraulic injection system and self-sharp cutting teeth, the key cutting teeth can achieve the purpose of joint rock breaking and make up for the pure mechanical cutting of the ordinary diamond bit and the passivation of the cutting teeth. And the defects such as poor clear rock can greatly improve the drilling speed.
2.4 “Gold” series and “Star” series drill bits
The "Gold" series of drill bits is a diamond full-drilling drill bit developed by Christensen in recent years. Its biggest feature is to greatly improve the life of the drill bit and the rate of mechanical drilling. The “Gold” series consists of fourteen different types of drill bits for different formations. The “Gold” series of drill bits have a unique design that makes them a high-tech leader in the diamond drill market.
The "Star" series of drill bits can easily adjust the caster angle and wear section of the cutting teeth to reduce their ingestion and reduce torque variations, making them suitable for use in high-angle wells and horizontal wells. The "Star" series diamond drill bit contains a new concept of the "Gold" series diamond drill bit.
2.5 Diamond drill bit for multiple sandwich formations
The Shengli Oilfield Drilling Technology Research Institute has developed a diamond drill bit suitable for multi-layered formations. The diamond drill bit has a unique cutting structure, with a diamond composite sheet as the main cutting tooth and a thermally stable polycrystalline diamond as the auxiliary cutting tooth. The two kinds of cutting teeth form a composite cutting structure in a certain processing form, which greatly improves the diamond bit. Application range.
3 Conclusion
The development of diamond bit technology has been around for more than 20 years, but the current pace of diamond bit design improvements is faster than ever. Because the application range of diamond drill bits is more and more widely, people expect higher and higher, which forces designers to continuously strive to innovate and develop new and more effective methods to optimize bit design and improve bit design. Developed a new type of drill bit. At present, the focus of diamond bit research has changed from therapeutic to preventive.
From the perspective of drilling trends at home and abroad, it is difficult to greatly increase the drilling speed under the existing drilling technology conditions, especially in special strata such as easy slope, affected by drilling parameters, the mechanical drilling speed is low, greatly Affected the construction period. The diamond drill has high mechanical drilling speed, large footage and long service life, which greatly improves the drilling speed and has the advantage of long life in deep wells. The use of diamond drill bits is the trend to accelerate exploration and development.
-All diamond tools can be ordered and fabricated!
-Henry Wang | Quote Manager
-WhatsApp:+86-13459035657
-Email: ceo@zdiamondtools.com
-Web www.zdiamondtools.com
Company Profile
Certifications
Company Team
Exhibition
Logistics
FAQ