Key words cubic boron nitride tool, diamond cutting tool|2019-09-30 09:56:50|Source China Superhard Materials Net
For a long time, cubic boron nitride was considered not to exist in nature until 2009, when scientists from the University of California, Riverside, Lawrence Livermore National Laboratory, and colleagues from Chinese and German research institutions, The mineral was found in the chrome-rich crust of the ancient oceanic crust about 306 km deep in the southern mountainous area of the Qinghai-Tibet Plateau, China. It formed crystals at a high temperature of about 1300 °C and a high pressure of 118,430 atmospheres.
What is CBN (cubic boron nitride)?
CBN (CubicBoron Nitride) is a man-made cubic boron nitride tool (CBN tool) first developed by General Electric (GE) in the United States under high temperature and high pressure conditions in the 1950s. Its hardness is second only to diamond. It is much higher than other materials, so it is collectively referred to as superhard material. Cubic boron nitride is synthesized by hexagonal boron nitride and catalyst under high temperature and high pressure. It is another new product that emerged after the advent of synthetic diamond.
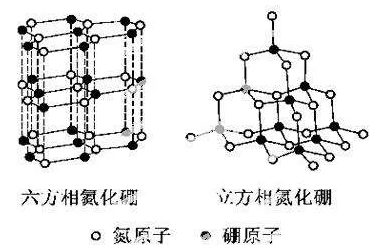
In the 1970s, the former Soviet Union, China, the United States, the United Kingdom and other countries successively developed the CBN sintered body, the polycrystalline Cubic Boron Nitride. Since then, PCBN has been used for cutting high-hardness iron, steel and other ferrous materials with its superior cutting performance.
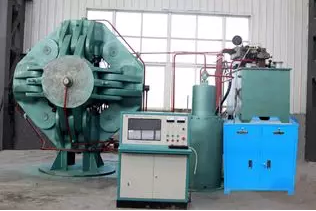
The bonding of PCBN tools can be summarized into three categories:
Metal bond, such as Ti, Co, Ni. Cu, Cr, W and other metals or alloys, softens at high temperatures, affecting tool life;
Ceramic bonding agents, such as Al2O3, are resistant to high temperatures, but have poor impact toughness and are prone to chipping and breakage of the tool;
A cermet binder, such as a solid solution formed of Co, Ni, or the like, such as a carbide, a nitride, or a boride, solves the disadvantages of the above two types of binders.
Performance and characteristics of CBN (cubic boron nitride) tool materials
High hardness and wear resistance
The microhardness of CBN single crystal is 8000~9000HV, which is the second highest hardness material known at present. The hardness of PCBN composite sheet is generally 3000~5000HV.
High thermal stability and high temperature hardness
The heat resistance of CBN can reach 1400~1500 °C, and oxidation does not occur at 1300 °C. The hardness at 800 °C is the normal temperature hardness of Al2O3/TiC ceramics. Therefore, high-hardness steel materials and heat-resistant alloys can be cut at high speed, and the bonding and diffusion wear of the cutters is small.
Has good thermal conductivity and has a low friction coefficient with steel
Flexural strength and fracture toughness between ceramic and cemented carbide
The thermal stability is much higher than that of synthetic diamond. It is still machinable at 1300 °C, has high oxidation resistance, and does not produce oxidation at 1000 °C. The chemical inertness of iron is much greater than that of synthetic diamond, and iron-based materials. It is not easy to chemically act at a high temperature of 1200 to 1300 ° C, but it will hydrolyze with water at about 1000 ° C, causing a large amount of CBN to be worn. Therefore, it is necessary to pay attention to the type of cutting fluid when wet cutting with a PCBN tool.
Due to the advantages of cubic boron nitride materials, it can rough and semi-finish hardened steel and chilled cast iron. At the same time, it can cut high-temperature alloys, thermal spray materials and other difficult materials at high speed.
Classification and structure of CBN (cubic boron nitride) tools
Cubic boron nitride can also be sintered with cemented carbide. This cubic boron nitride sintered body has a flexural strength of 1.47 GPa and can be used for many times. There are two types of cubic boron nitride knives: integral polycrystalline cubic boron nitride cutters and cubic boron nitride composite blades. The cubic boron nitride composite blade is formed by sintering a cubic boron nitride having a thickness of about 0.5 mm in a cemented carbide sintered body.
Integral
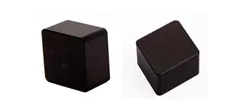
Mosaic
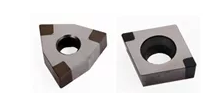
Compound
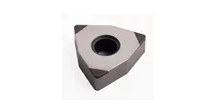
Application of CBN tools
Divided by processing material
High hardness cast iron (hardness HSD75 or higher), such as high chromium cast iron, alloy cast iron, nickel hard cast iron, white cast iron and other materials. Typical components are rolls and industrial pumps.
High hardness steel parts (hardness HRC45 or more), such as high manganese steel, high speed steel, hardened steel, etc. Typical components include rolled wall, high speed steel rolls, hardened gears/gear shafts, bearings, ball screws, molds, etc.
Ordinary gray cast iron (HT150/200/250/300)
Such as engine block, cylinder head, brake disc, brake drum, pulley, clutch platen, etc. are all ordinary gray cast iron.
Other difficult materials
Such as powder metallurgy, high-temperature alloy materials, and nickel-based, iron-based, cobalt-based high-hardness surfacing, spray welding, laser cladding, thermal spraying materials.
By application industry
Mining machinery industry
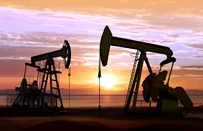
Steel roll industry
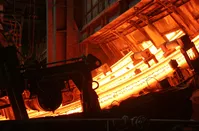
Aerospace industry
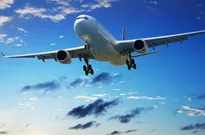
Energy industry
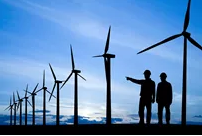
Automobile industry
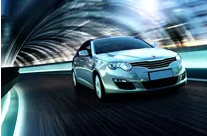
Application of CBN tools
Heavy duty cutting
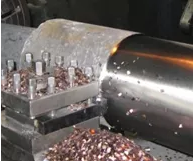
High speed cutting
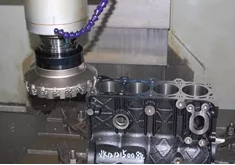
Car grinding
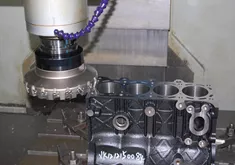
Dry cutting
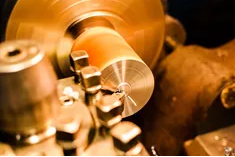
Cutting parameters of CBN tools
Conventional cutting parameters
When roughing, try to ensure a high metal removal rate and the necessary tool durability. Therefore, it is generally preferred to select the largest cutting depth ap, and secondly select a larger feed amount f, and finally determine according to the tool durability requirements. The right cutting speed. When finishing, the machining accuracy and surface quality requirements of the workpiece should be guaranteed first. Therefore, the smaller feed rate f and the cutting depth ap are generally selected, and the higher cutting speed υc is used as much as possible.
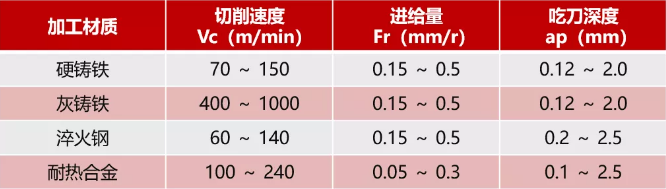
Calculation formula for turning machining
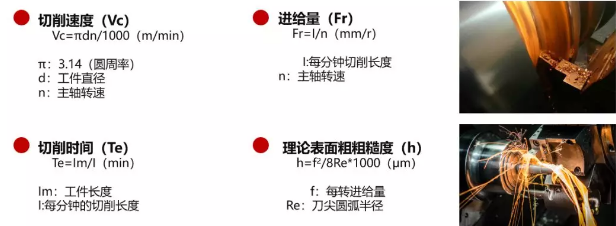
Calculation formula for milling
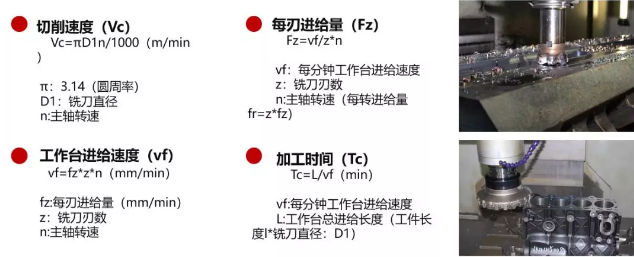
Advantages of CBN tools
Judging from the point of use
Good impact resistance, especially in the roughing field, it does not chip and not break when used. This is the most basic guarantee for the safety of CBN tools.
Good wear resistance, high efficiency machining, and the ability to replace carbide tools and ceramic inserts at low cost, which is the economical guarantee for the use of CBN tools.
Judging from the manufacturing point of view
High purity, high purification rate raw materials, reliable and standardized embryo body synthesis process, these two directly determine the performance of CBN tools. Of course, this is also the biggest reason for the uneven price of CBN tools on the market.
Grinding, because CBN tools do not have complex grooves and coatings like cemented carbide inserts, the performance depends mainly on the tool body performance, and the grinding process and precision directly determine the microscopic properties during cutting. Therefore, although the cost of using peripheral grinding tools is much improved, the quality and durability of CBN tools will be upgraded.
In addition to dimensional accuracy and surface quality, the most prone to waste in the production of CBN tools is microscopic defects under SEM. The microscopic defects that are invisible to the naked eye at the cutting edge are the fuses of the chipping edge during the use of the CBN tool, which is easy to cause the problem of tool knives when used.
Wear form of CBN tool
Wear form in continuous cutting
Rake wear
The most common form of wear is the friction between the tool and the hard particles in the workpiece. Severe wear can result in poor surface roughness and dimensional accuracy of the workpiece being machined, replacing the new CBN insert.
Crescent tooth wear
Occurs in the rake face of the insert, caused by chemical reactions between the workpiece material and the cutting tool. The crater wear can cause the chip treatment to deteriorate, affecting the quality of the machined surface, and excessive crater wear can weaken the cutting edge and can cause breakage.
Pressure surface wear
The main reason is that the cutting speed is too fast, the feed rate is too large, and the back angle of the tool is too small to cause the pressure surface to wear.
Boundary wear
The main reason is that the main declination is too large, the feed is too large, and the cutting speed is too low, causing the boundary to wear.
Damaged form in interrupted cutting
Crushing
This is a common form of breakage when CBN tools are used to interrupt steel and cast iron. It is a small gap created in the cutting edge, with a few small gaps in the blade or a small piece that has collapsed. For example, a micro-cracking tool can interrupt cutting within the allowable wear limit, and the tolerance is replaced.
Peeling off
When milling steel and cast iron end faces, shell-like spalling often occurs on the rake face. In such cases, the blade can be passivated with a negative chamfer and a cutting edge by increasing the cutting speed and reducing the feed rate.
fracture
The damage form that often occurs when cutting workpieces intermittently. This is due to excessive impact load when cutting high-hardness workpieces intermittently, and early damage after short-time cutting. Although the cutting conditions are appropriate, after cutting for a long time, there is no timely tool change. A large piece of fracture occurred due to fatigue of the tool material.
crack
After long-term intermittent cutting, the CBN tool has mechanical fatigue cracks parallel to the cutting edge caused by mechanical impact, and cracks perpendicular to or inclined to the cutting edge due to thermal shock. When these cracks are continuously expanded and merged, the blade is broken or broken.
-All diamond tools can be ordered and fabricated!
-Henry Wang | Quote Manager
-WhatsApp:+86-13459035657
-Email: ceo@zdiamondtools.com
-Web www.zdiamondtools.com
Company Profile
Certifications
Company Team
Exhibition
Logistics
FAQ