Polishing concrete after it sets is not only possible but a common method for enhancing the beauty and durability of concrete surfaces. This process can transform a dull, rough concrete slab into a smooth, shiny surface that is both aesthetically pleasing and functional. However, several factors must be considered to ensure the effectiveness and safety of the polishing process.
Factors to Consider
- Concrete strength: The strength of concrete is a key factor in determining whether it can be effectively polished. Concrete with higher strength is generally better suited to polishing because it can withstand the grinding process without compromising its structural integrity. Concrete with lower strength may require a more cautious approach and a shallower polishing depth to avoid damage.
- Surface condition: The existing condition of the concrete surface will affect the polishing process. If the surface is heavily stained, cracked, or uneven, additional preparation may be required before you begin polishing. This may include cleaning, filling cracks, and sanding high spots.
- Polishing techniques: Depending on the specific characteristics of the concrete, different polishing techniques may be required. For example, some surfaces may be suitable for wet polishing, which uses water to reduce dust and heat, while other surfaces may be more suitable for dry polishing.
- Safety precautions: As with any construction process, safety is of paramount importance. Operators should wear appropriate personal protective equipment, including goggles, gloves, and dust masks, to protect against dust and debris generated during the polishing process. It is also important to ensure that the workplace is well ventilated to minimize exposure to harmful particles.
Properties of Concrete After Solidification
Solidification process
Once cement, water, aggregates, and any additives are mixed, concrete begins to set. This process involves hydration, where water reacts with cement particles to form a hardened structure. Over time, concrete increases in strength and hardness, transforming from a plastic to a solid state. The rate of setting and ultimate properties of concrete depends on a variety of factors, including mix design, environmental conditions, and curing method.
Key properties of cured concrete
- Surface hardness: One of the most notable properties of set concrete is its surface hardness. As concrete cures, it develops a hard outer layer that can withstand severe wear and tear. This hardness is critical in applications where the surface will be subject to foot traffic, machinery or other forms of pressure.
- Abrasion resistance: The abrasion resistance of concrete increases as it solidifies. A well-cured concrete surface resists abrasion and impact, making it suitable for polishing. This property is especially important in commercial and industrial settings where floors are subject to heavy use.
- Porosity and density: The porosity of concrete affects its durability and strength. Cured concrete generally has a low porosity content, which affects its density and overall strength. However, porosity will vary depending on mix design and curing conditions. Lower porosity generally results in better moisture resistance and durability performance.
- Surface texture: The surface texture of concrete after it sets can vary greatly depending on the finishing techniques used during the pouring and curing process. The smoother the surface, the easier it is to polish, while the rougher the texture, the more likely it is that you will need additional sanding to achieve the desired effect.
- Chemical resistance: Cured concrete exhibits varying degrees of chemical resistance, depending on the mix design and any additives used. This property is critical in environments where concrete may be exposed to harsh chemicals, as it can affect the longevity and appearance of the polished surface.
Working Principle of Polishing Machine
Polishing machines are essential tools in the construction and renovation industries, especially for improving the appearance and durability of concrete surfaces. These machines use a simple yet effective mechanism to grind and polish using a disc that spins at high speeds. Understanding how a polishing machine works can help users achieve the best results in their concrete finishing projects.
The core components of the polishing machine
- Disc for grinding concrete: The main component of a polishing machine is the grinding disc, which is loaded with abrasive materials. These abrasive materials have different particle sizes to achieve different degrees of grinding and polishing. Coarse sand is used for initial grinding to remove flaws, while fine sand is used for polishing to obtain a smooth surface.
- Motor: The motor powers the polisher, allowing the grinding disc to spin at high speeds. The speed of rotation is critical because it affects the efficiency of the grinding and polishing process. Most polishers allow the user to adjust the speed to suit the specific requirements of the concrete surface being treated.
- Weight and pressure mechanism: Many polishers are designed to apply constant pressure to the grinding disc on the concrete surface. This weight helps ensure effective grinding and polishing while preventing excessive wear on the disc itself.
Polishing process
The polishing process involves several key steps, each of which affects the overall efficiency of the machine:
- Initial grinding: When a polisher is first used on a concrete surface, the operator typically starts with a coarse grit grinding disc. This initial stage focuses on removing any surface imperfections such as rough spots, stains, or uneven areas. The high speed of the disc combined with the abrasive effectively smooths these irregularities.
- Grind the surface: As the operation progresses, the operator will switch to finer grinding wheels. This step is critical to further refine the surface. The abrasives on the finer grinding wheels gradually refine the concrete, reducing the roughness and preparing it for the final polishing stage.
- Polishing: In the final stage, ultra-fine grinding wheels are used to polish the concrete surface. The high-speed rotation and fine abrasives work together to create a smooth surface. During this stage, the friction created by the polishing disc also helps to densify the concrete surface, enhancing its impermeability and overall durability.
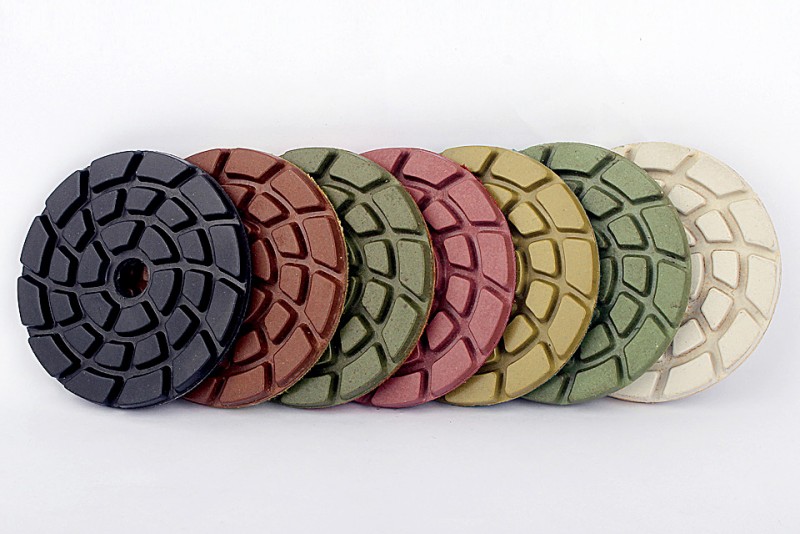
Benefits of using a polishing machine
- Improved appearance: The main benefit of using a polisher is that it enhances the aesthetics of the concrete surface. Polished concrete floors have a sleek, modern look that can enhance the overall design of a space.
- Improved durability: The polishing process not only improves the appearance but also enhances the strength of the concrete. The densification achieved during the polishing process makes the surface more resistant to wear, moisture, and weathering, thereby extending the service life of the concrete.
- Easy to maintain: Polished concrete surfaces are easier to clean and maintain. The smooth surface prevents dirt and grime from accumulating, making daily cleaning more efficient.
- Enhanced Performance: Polished concrete surfaces exhibit improved performance characteristics, including improved slip resistance and reduced dust flotation, making them suitable for a variety of applications from residential to industrial settings.
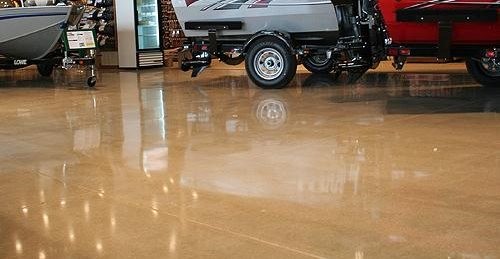
Polished Concrete Construction Precautions
1. Strength assessment
Before beginning the polishing process, it is critical to assess the strength of the concrete. The concrete must reach sufficient hardness to withstand grinding and polishing without suffering surface damage or spalling. Performing a compressive strength test helps determine if the concrete is ready for polishing. If the concrete is still curing or has not yet reached the required strength, it is recommended to postpone the polishing process to avoid compromising the surface integrity.
2. Surface treatment
The condition of the concrete surface plays a major role in the effectiveness of the polishing process. If the surface is contaminated with oil, dirt, impurities or old coatings, it must be thoroughly cleaned before polishing. This may involve using a degreaser, high pressure washing or mechanical scrubbing to remove any unwanted material. A clean surface ensures that the polishing process will be able to effectively remove imperfections and achieve the desired effect.
3. Choose the right polishing process and equipment
Selecting the right polishing process and equipment is essential to achieving the best results. The choice of polishing method should be based on the specifics of the concrete and the desired outcome. For example, a floor that requires high aesthetics may require multiple polishing stages using abrasives of different particle sizes. Starting with a coarser grit to remove imperfections and then gradually transitioning to finer grits will help achieve a smooth, shiny surface. Additionally, using the right type of polisher, whether planetary or rotary, can significantly impact the efficiency and quality of the polishing process.
4. Security Measures
Polishing concrete creates a lot of dust and noise, so safety precautions are essential. Operators should wear appropriate personal protective equipment, including dust masks, goggles, and ear plugs, to prevent inhalation of dust and exposure to loud noises. It is also important to ensure that the polishing machine is operated according to the manufacturer's guidelines to prevent accidents. Adequate ventilation in the workplace can help minimize dust accumulation and improve air quality.