Improving the Quality of Diamond Tools
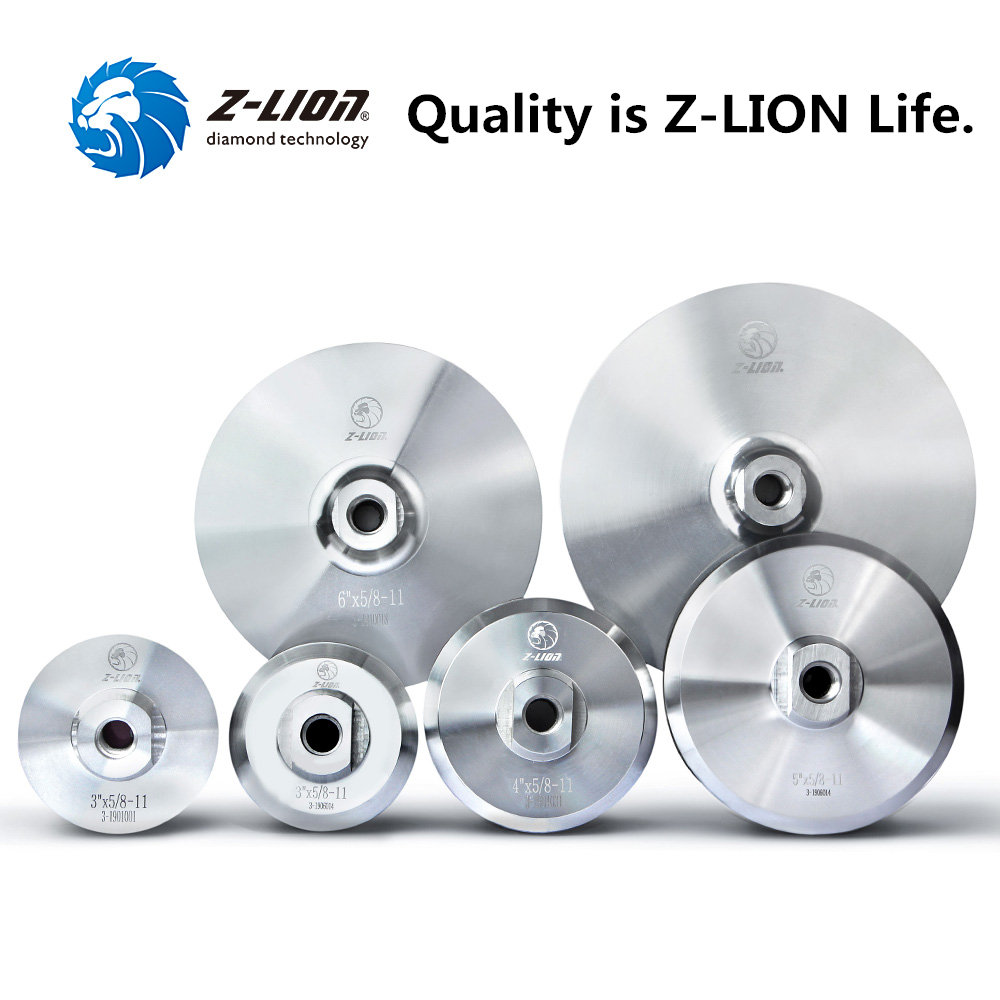
Introduction
Welcome to our article on improving the quality of diamond tools. In this comprehensive guide, we will explore various effective ways to enhance the performance and durability of diamond tools. Diamond tools have become increasingly popular due to their superior hardness and abrasion resistance compared to traditional abrasive materials like corundum and silicon carbide.
Diamond tools offer numerous advantages, including high grinding efficiency, low grinding force, and long lifespan. They are widely used in industries such as construction, woodworking, automotive, and engineering ceramics processing. However, to maximize the benefits of diamond tools, it is crucial to adopt certain techniques and technologies during the manufacturing process.
In this article, we will discuss seven effective methods for improving the quality of diamond tools. These include adopting high hardness diamonds, plating metal elements for improved hold, using ultrafine and pre-alloyed powder, implementing good granulation technique, utilizing vacuum protection atmosphere hot pressing technique, applying hot isostatic press and high temperature brazing technique, and utilizing laser welding technique.
By incorporating these techniques, manufacturers can enhance the quality, performance, and longevity of diamond tools. Whether you are a professional in the construction industry or a DIY enthusiast, this article will provide valuable insights into maximizing the efficiency and effectiveness of diamond tools.
So, let's dive into the details and discover how these techniques can revolutionize the world of diamond tools.
Adopting High Hardness Diamonds
When it comes to improving the quality of diamond tools, one effective approach is to adopt high hardness diamonds in the manufacturing process. The quality, grit, and concentration of the diamonds used play a crucial role in determining the overall quality of the diamond tools.
In recent years, there have been significant advancements in the production of high hardness diamonds. China's hinged cubic press machine, for example, has successfully produced 20/30 big grit high hardness diamonds. These diamonds offer a combination of superior quality and competitive pricing, making them an attractive option for manufacturers in the global market.
By incorporating high hardness diamonds into the manufacturing process, manufacturers can enhance the performance and durability of their diamond tools. These diamonds provide exceptional hardness, wear resistance, and low friction coefficient, giving the tools a cutting edge advantage. Additionally, the use of high hardness diamonds can contribute to the longevity of the tools, reducing the need for frequent replacements.
With the availability of high hardness diamonds in the market, manufacturers now have a viable option to improve the quality of their diamond tools. By adopting these diamonds, they can ensure that their tools deliver superior performance, longevity, and value to their customers.
Plating Metal Elements for Improved Hold
When it comes to improving the quality of diamond tools, one effective method is to plate metal elements onto the diamonds. This technique enhances the tools' hold on the diamonds, preventing them from falling off prematurely. Additionally, it results in sharper and more durable diamond tools.
The plating process involves using metal elements such as chromium (Cr), nickel (Ni), titanium (Ti), tungsten (W), and others to create a carbide alloy on the interface between the diamonds and the tool's bond. This carbide alloy improves the chemical bonding and metallurgical combination of the diamonds and the metals in the tool's bond.
There are several reasons why plating metal elements onto diamonds is beneficial. Firstly, the plated metals can prevent the oxidation, graphitization, and hot corrosion of the diamonds under certain temperature and pressure conditions during the sintering process. Secondly, the plated metals contribute to the formation of a carbide alloy, which enhances the hold of the diamonds to the tool's bond. Lastly, the friction of the diamonds is improved after plating with these metals.
By utilizing the plating technique, manufacturers can achieve diamond tools with superior quality and performance. This method not only ensures the longevity of the diamonds on the tools but also provides a cost-effective solution in the world market. With the improved hold and enhanced properties, diamond tools plated with metal elements offer a reliable and efficient solution for various cutting and grinding applications.
Using Ultrafine and Pre-Alloyed Powder
In order to further enhance the quality of diamond tools, the use of ultrafine powder and pre-alloyed powder in the tools' bond has proven to be highly effective. Ultrafine powder offers several advantages, including a decrease in the temperature of sintering and an increase in hardness. This results in improved grinding quality and high precision.
Pre-alloyed powder, on the other hand, prevents the loss and segregation of metals with low melting points. It also enhances the elastic limit and yield strength of sintered products, ultimately improving the tools' hold to diamonds. Additionally, the use of pre-alloyed powder reduces the temperature of sintering and decreases the time of heat preservation.
By incorporating ultrafine and pre-alloyed powder in the manufacturing process, diamond tools can achieve a longer lifespan and a longer dressing period. This significantly increases work efficiency and reduces labor intensity. Moreover, the comprehensive cost of processing each workpiece is lowered.
Overall, the utilization of ultrafine and pre-alloyed powder in diamond tools offers numerous benefits, including improved grinding efficiency, high wear resistance, and increased productivity. These advancements contribute to the overall quality and performance of diamond tools, making them an essential component in various industries such as construction, woodworking, and automotive spare parts processing.
Implementing Good Granulation Technique
When it comes to improving the quality of diamond tools, one effective method is implementing a good granulation technique in the production of segments. This technique offers a range of benefits that can enhance the overall performance and durability of the tools.
First and foremost, a good granulation technique helps reduce the segregation of diamonds, ensuring that they are distributed more evenly throughout the tool. This improved distribution enhances the cutting performance of the segments and increases the mobility of the powder. As a result, the cold pressing technique is more effective, leading to higher-quality tools.
Additionally, this technique helps to minimize the dust hazards to workers. By distributing the diamonds more evenly, the granulation process reduces the likelihood of diamond particles becoming airborne during production. This not only improves the safety of the work environment but also ensures that the diamonds are utilized to their fullest potential.
Furthermore, the even distribution of diamonds achieved through good granulation enhances the overall cutting performance of the segments. With a more uniform distribution of diamonds, the tools are able to deliver sharper and more precise cuts. This not only improves the efficiency of the tools but also extends their lifespan, resulting in cost savings for manufacturers.
In conclusion, implementing a good granulation technique in the production of diamond tools is a crucial step in improving their quality. This technique allows for a more even distribution of diamonds, enhances cutting performance, reduces dust hazards, and ultimately leads to more durable and efficient tools. Manufacturers should prioritize the implementation of this technique to maximize the performance and value of their diamond tools.
Utilizing Vacuum Protection Atmosphere Hot Pressing Technique
When it comes to improving the quality of diamond tools, one technique that has proven to be effective is the utilization of the vacuum protection atmosphere hot pressing technique. This technique is a key step in the manufacturing process of diamond saw blades and has a significant impact on the overall quality of the product.
By using a vacuum protection atmosphere during the hot pressing process, manufacturers are able to control the segment density, hardness, and cutting performance of the saw blades. The vacuum environment helps to eliminate any impurities or contaminants that may affect the quality of the diamonds or the bonding material.
Additionally, the use of a protection atmosphere ensures that the sintering process is carried out under optimal conditions, resulting in improved segment density and hardness. This, in turn, enhances the cutting performance of the saw blades and extends their lifespan.
The vacuum protection atmosphere hot pressing technique also plays a crucial role in the technical performance of the sintering equipment. By maintaining a controlled environment, manufacturers can minimize production costs and ensure consistent product quality.
Overall, the utilization of the vacuum protection atmosphere hot pressing technique is a valuable tool in the quest for improving the quality of diamond tools. Its ability to enhance segment density, hardness, and cutting performance makes it an essential step in the manufacturing process. By implementing this technique, manufacturers can produce diamond tools that are sharper, more durable, and of higher quality.
Applying Hot Isostatic Press and High Temperature Brazing Technique
When it comes to improving the quality of diamond tools, one technique that has proven to be effective is the application of hot isostatic press (HIP) and high temperature brazing. This method offers several advantages that contribute to the overall performance and durability of diamond wire saws.
By utilizing the HIP technique, the porosity of the diamond wire saws can be significantly reduced. This results in improved density, hardness, toughness, and overall performance of the saw's beads. The HIP process ensures that the beads have a higher resistance to wear and can withstand the demands of cutting through tough materials.
In addition to the HIP technique, the use of high temperature brazing further enhances the quality of diamond wire saws. This technique allows for a strong hold to the diamonds, ensuring that they remain securely in place during operation. The brazing process also promotes a chemical bonding and metallurgical combination between the diamonds and the tool's bond, resulting in a more durable and efficient cutting tool.
By incorporating these techniques into the manufacturing process of diamond wire saws, manufacturers can achieve significant improvements in performance and cost-effectiveness. The use of HIP and high temperature brazing techniques not only extends the useful life of the diamonds, but also increases cutting speed and reduces production costs.
In conclusion, the application of hot isostatic press and high temperature brazing techniques is a crucial step in enhancing the quality of diamond tools. These techniques improve the overall performance, durability, and cost-effectiveness of diamond wire saws, making them a preferred choice for various cutting applications.
Utilizing Laser Welding Technique
Laser welding has revolutionized the manufacturing process of diamond tools, offering a precise and reliable method for joining the saw blade's body and its segments. With the use of laser welding machines, the traditional manual mode of fixing the segments is replaced with a fully automatic mode, resulting in increased accuracy and efficiency.
The benefits of laser welding in diamond tool manufacturing are numerous. Firstly, laser welding machines provide a high power output, ensuring a strong and durable weld. Additionally, they consume less gas, resulting in lower running costs and maintenance requirements. The quality of the beam produced by laser welding machines is exceptional, guaranteeing a superior weld every time.
By utilizing laser welding techniques, manufacturers can achieve a higher level of precision in the welding process. This leads to improved product quality and performance, as well as increased customer satisfaction. Laser welding also offers the flexibility to weld different types of diamond tools, including saw blades, drill bits, and grinding wheels.
Furthermore, laser welding machines have the capability to weld various materials, including metals and non-metals. This versatility allows manufacturers to create diamond tools that are suitable for a wide range of applications, from construction and woodworking to automotive and aerospace industries.
In conclusion, the utilization of laser welding technique in the manufacturing of diamond tools has significantly enhanced the quality and performance of these tools. With its precision, reliability, and versatility, laser welding has become an indispensable tool for diamond tool manufacturers, ensuring the production of high-quality and durable tools that meet the needs of various industries.
Xiamen ZL Diamond Technology Co., Ltd. is a New Three Board listed enterprise, engaged in the development and application of diamond new material. We innovate new material and application in diamond super hard field, strive to offer advanced diamond new material application products and solution.
We mainly produce diamond tools including diamond polishing pads,diamond core drill bit, diamond wire saw, etc. Our products are widely used in the cutting, grinding and polishing field of stone, ceramic, glass, concrete.
For twenty years, we keep on focusing on the innovation of our products, make our efforts on brand management and marketing operation, keep raising high level of our brand and market ratio, get highly recognized by the diamond tools industry. We are honored as “National Intellectual Property Advantage Enterprises”, “Fujian Innovative Enterprises”, drafting unit of “Diamond Flexible Polishing Pads Industrial Standard”. At the same time, many products are first innovated by us. By far, we own 63 of domestic and international patents. Our products are welcome in the market of Europe, North and South American, South-East Asia, Middle Asia, etc. Good reputation has won praise and trust from home and abroad.
Contact us, you will get more than what you see.
-All diamond tools can be ordered and fabricated!
-Henry Wang | Quote Manager
-WhatsApp:+86-18030177538
-Email: ceo@zdiamondtools.com
-Web www.zdiamondtools.com
Company Profile