Keywords milling cutter milling inserts | 2020-03-18 09: 11: 13 | Source Sandvik Coromant
What depends on the formation of the milled surface? The resulting milled surface can be axial, radial, or complex, depending on the type of tool and process used.
Axially generated surface
The shape of the bottom of the blade determines the quality of the resulting surface. Tip arcs (RE) sometimes produce sharp tips. The size of the tip depends on the arc radius and feed.
Blades with parallel blades (BS) are capable of machining flat surfaces. Based on the axial tolerances and runout of the milling cutter, the most protruded insert creates the final surface.
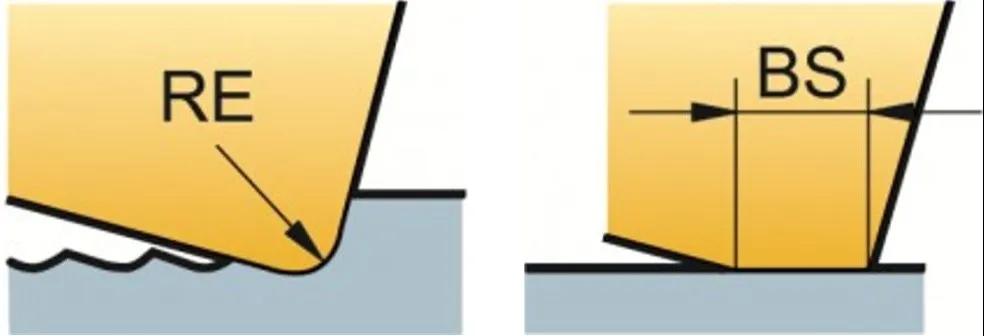
Tip radius (RE) and parallel blade (BS)
In order to produce the best milling surface quality, it is important to ensure that the feed per revolution (fn = fz × zn) is less than 80% of BS.
As the cutter diameter increases (and for ultra-dense tooth cutters), the number of teeth and feed per revolution increase, requiring a larger BS. Once the feed per revolution exceeds the width of the parallel blade, the axial runout of the milling cutter will affect the surface quality.
For best milling surface quality:
1) Use Wiper (sharpening) blades or other milling inserts with a shaving edge that are at least 25% larger than fn
2) Use metal-ceramic blades for better finish
3) Use cutting fluid to avoid sticking
Wiper Blade
Sharpening edges or long parallel blades enable finishing with larger diameters. The sharpening edge is higher than the standard blade, ensuring that the sharpening edge produces the final surface. The maximum fn should not exceed 80% of the BS.
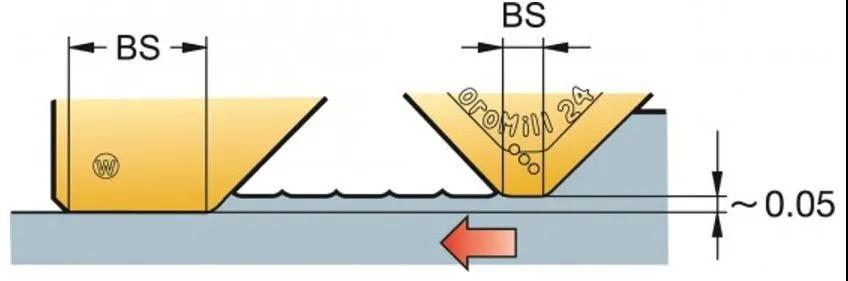
Round blade
Round inserts or inserts with a large tip radius can achieve extremely high productivity but cannot produce high-quality surfaces. The larger the cutter diameter, the worse the surface quality.
02. Radially generated surface
When using end mills, square shoulder mills, or three-sided cutters, radial surfaces are created. For radially generated surfaces, the contours of the tool are machined.
Each tooth produces a tip (h), where the tip width is equal to the feed amount fz per tooth, and the tip depth is determined by the relationship between the cutter diameter and fz. The theoretical calculation of the spire size is minimal.
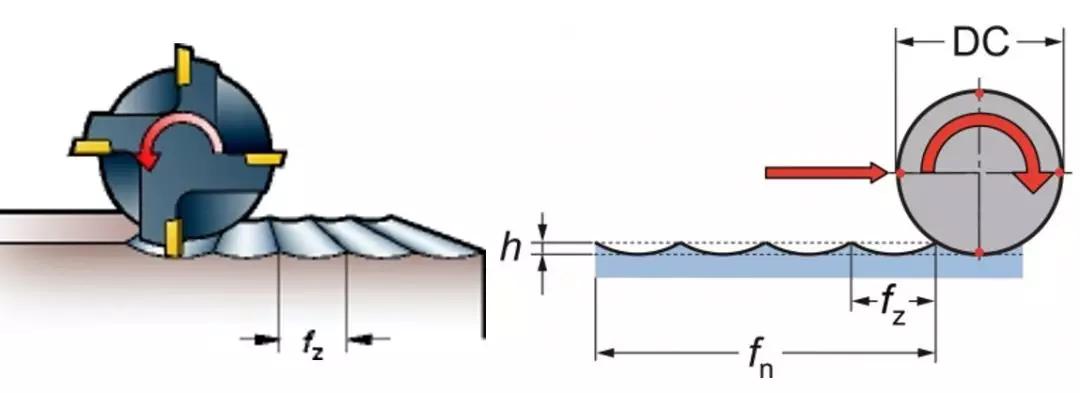
03. Complex surface generation
When using a ball end mill, a complex surface is created.
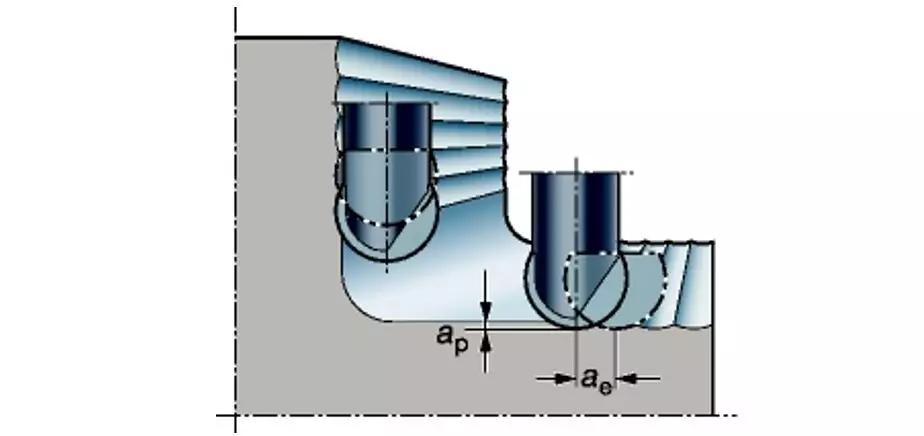
-All diamond tools can be ordered and fabricated!
-Henry Wang | Quote Manager
-WhatsApp:+86-13459035657
-Email: ceo@zdiamondtools.com
-Web www.zdiamondtools.com
Company Profile
Certifications
Company Team
Exhibition
Logistics
FAQ