Keywords diamond welding | 2020-01-10 10: 20: 16 | Source Welding Wang
Because diamond has extremely high hardness and good abrasion resistance, it is an ideal material for hard materials such as crushed rock. Due to the high interfacial energy between diamond and general metals and their alloys, they have poor wettability with metals and their alloys, and are easily graphitized at high temperatures, resulting in poor diamond weldability. The main difficulties in connecting diamond to metal are: first, the welding temperature is limited by the graphitization temperature of diamond, it is difficult to achieve a true chemical-metallurgical combination, and the strength of the welded joint is very low; second, most low-carbon steel matrix materials or carcasses The material is difficult to infiltrate or cannot be soaked into the diamond, and the substrate's ability to grasp the diamond is very poor after welding, which causes the diamond to detach during the use of the product, and the excellent performance of the diamond cannot be fully exerted. Third, the linear expansion coefficient of the diamond is lower than most metal materials Or alloys are prone to cracks during welding.
Therefore, traditional diamond tools are generally manufactured by chemical plating or low-temperature brazing. The metallurgical combination of diamond and substrate is not achieved, the welding strength is low, the performance is poor, and the use of diamond is very low. Only by comprehensively solving the welding difficulties of the above three aspects can we truly exert the high performance of diamond. At present, diamond high-temperature welding technology has attracted the attention of related welding technicians, and it may be useful to learn from welding.
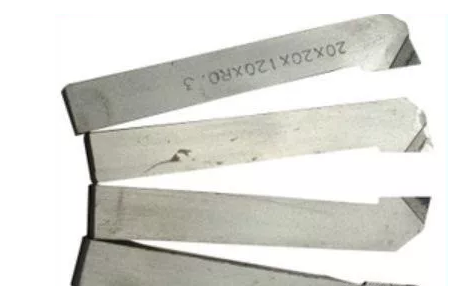
During the use of diamond tools, the performance of the carcass material is one of the key factors affecting the performance of diamond tools. Foreign studies have found that the use of diamond alloy pre-alloying technology, diamond tools use better. Domestic technology in this area has only been used in small amounts on sintered diamond products, and the use of pre-alloy powder technology for welding carcass alloys has rarely been reported.
Because diamond is extremely easy to graphitize at high temperatures, a low-melting carcass material is spray-welded on a low-carbon steel substrate when welding.The performance requirements are: (1) it can form a low melting point with a diamond metallized surface alloy Eutectic to reduce the welding temperature of diamond and avoid graphitization; (2) it can have good weldability with low carbon steel substrate; (3) it has higher hardness and can effectively support diamond; (4) with diamond The difference between the expansion coefficients of the metalized transition layer TiC layer and the low carbon steel matrix is small to reduce welding stress and avoid welding cracks. In order to meet the requirements of the above four aspects, the carcass alloy can use nickel and cobalt as the main components, and then add an appropriate amount of titanium, a trace amount of rare earth and a small amount of boron, silicon, etc., while reducing the melting point of the alloy, Can improve alloy fluidity and wettability.
The pre-selected alloy can be pre-alloyed with metal powder, that is, it is first smelted into an alloy according to the design formula, and then atomized into a carcass powder with a desired particle size. The test proves that the pre-alloying method can be used to prepare pre-alloyed powders with uniform structure, low melting point, easy sintering, and good wetting and adhesion to diamond. It is spray-welded on the steel substrate and heated to a temperature slightly higher than the liquidus temperature of the pre-alloyed powder during remelting. After the pre-alloyed powder is melted, it is metallurgically combined with diamond, which does not occur when welding mechanically mixed powder matrixes. Defects such as density segregation, melting and enrichment of low-melting metals first, easy oxidation or volatile metals are difficult to control during remelting, and are conducive to the stability of the welding process.
In order to reduce the graphitization tendency of diamond, diamond is required to have the best thermal stability. It can be known from research that the thermal stability of diamond increases significantly with the weakening of diamond magnetism under general conditions. In view of the close relationship between the magnetic properties of diamond and its thermal stability, diamonds that can be used for welding are preferably selected by measuring their magnetic properties.
In order to improve the wettability and weldability of metals and their alloys to diamonds, previous research has mostly focused on the use of diamond surface plating technology. This process only wraps a thin layer of metal on the surface of the diamond, and does not generate metal carbides on the diamond. Transition layer.
In order to achieve better welding, the diamond surface metallization process is adopted.First, the diamond needs to be cleaned with dilute hydrochloric acid and acetone and dried at 150 ° C, then mixed with titanium powder in a crucible, and then BaCl2 + NaCl is used as Mainly, add a small amount of chlorine-based mixed salt to cover it, heat the box resistance furnace to 100 ° C ~ 150 ° C above the melting point of the mixed salt, then place the crucible in the furnace, keep it for 0.5 ~ 1h, and then cool it with the furnace and take it out. The crucible is placed in boiling water to dissolve the salt to obtain titanium-coated diamond, and this diamond surface metallization process makes the diamond surface uniform and complete. The test proved that the main surface of diamond was titanium.
The diamond infiltrated by the salt bath was placed in a vacuum furnace, heated at 900 ° C (1h) under a vacuum of 1.33 × 10-4P2a, and then cooled with the furnace. Because titanium is a strong carbide-forming element, it combines with carbon atoms on the diamond surface during heating to form TiC nuclei and gradually grow until a thin TiC transition layer is formed on the diamond surface.
The use of thermal insulator can protect diamond from thermal erosion during high temperature welding and avoid high temperature graphitization of diamond. Related research shows that the thermal conductivity of TiH2 powder is 0.5W / (mK), and the enthalpy change of the TiH2 decomposition reaction is 125.4kJ / mol. Use it to absorb and take away the heat around the diamond, which can shield the carcass from melting. The diamond is overheated and graphitized. Some organic polymers can be decomposed into alkanes, hydrocarbon small molecular gases and free carbon at high temperature, and the heat absorbed is about 105kJ / kg.
If the amount of organic thermal insulator applied in 1kg alloy is 10g, the theoretical heat absorption of the insulator can reach 1000kJ during the formation of metal droplets, and the formation of 1kg superheated molten metal droplets (1000 ℃) requires heat. About 3000kJ. Therefore, the thermal insulation agent can reduce the temperature of the metalized diamond and reduce the overheating of the carcass, which can effectively prevent the graphitization caused by the overheating of the diamond. In addition, the titanium remaining from the decomposition of metal hydride TiH2 can form a TiC layer with the residual carbon in the pyrolysis of organic polymers to play a role in metallizing diamond.
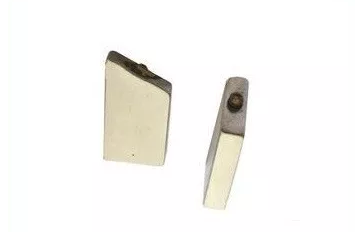
Therefore, the metalized diamond is washed first, and then a thin layer of TiH2 powder is used to coat the surface of the metalized diamond, and then the organic polymer is coated, which can achieve a suitable coating thickness and good uniformity, and it should be dried after coating. In addition to moisture. Due to the low cost of coating, it can be applied to industrial production, pre-alloying the carcass alloy, and then spray-welded on the low-carbon steel substrate. After the spray-welded layer is ground and cleaned, the coated diamond is bonded to the glass with water glass. Spray welding on the layer and drying. Welding with oxyacetylene gas welding and welding with a carbonized flame, so that the welding place of diamond and carcass is in a reducing atmosphere, which is beneficial to prevent diamond graphitization.
Welding diamond should pay attention to slow cooling after welding to avoid welding cracks. The most important indicator of the quality of diamond and carcass welding is the wear resistance of the weldment. Under the same conditions, the wear of the sample after welding by other traditional welding processes is about 330g, and the wear of the sample by high temperature welding technology is 40.5g. It can be seen that the new welding process of high-temperature welding technology maintains the high wear resistance of diamond. The above views are for reference only.
-All diamond tools can be ordered and fabricated!
-Henry Wang | Quote Manager
-WhatsApp:+86-13459035657
-Email: ceo@zdiamondtools.com
-Web www.zdiamondtools.com
Company Profile
Certifications
Company Team
Exhibition
Logistics
FAQ