Core Tip: In order to improve the welding strength of diamond circular saw blades, laser welding is used. However, due to the large difference between the material of the diamond blade transition layer and the matrix material, the requirements for the matrix of the laser-welded diamond circular saw blade are required. high. This paper describes the material and requirements for the laser-welded diamond circular saw blade transition layer.
Theoretically, the laser welding method is easy to obtain high weld strength. However, in the production of diamond saw blades, since the transition layer (welding layer) material of the diamond cutter head and the saw blade base material are different, and the performance difference between the two is large, the welding between them is a heterogeneous material welding, which must be reasonable. The welding process parameters are selected and the process is strictly controlled to obtain high weld strength. The base material of the saw blade is generally determined. Usually, it is several steel materials such as 30CrMo/28 CrMo, 50Mn2V, and 65Mn. The design of the transition layer of the saw blade is the key to ensure the laser welding strength of the saw blade. The transition layer material should not only have the welding performance as close as possible to the base material, but also must match the carcass of the working layer of the cutter head. Generally, the base material has a large difference from the material of the working layer of the cutter head, so designing the transition layer of the saw blade has a considerable difficulty.
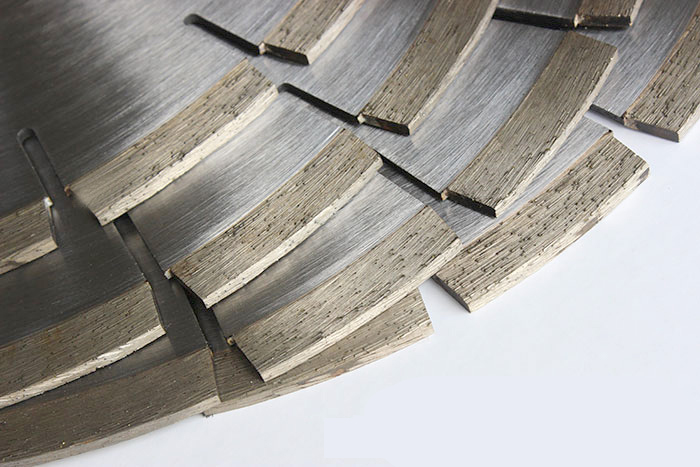
The characteristics of laser welding are: high energy density of the laser beam after focusing (105~107W/cm2), fast heating rate, fast welding rate and small heat affected zone, but the laser welding seam has high temperature and large temperature gradient.
Therefore, the basic requirements for the laser welding transition layer are:
(1) The boiling points of the elements in the transition layer should be similar to prevent the formation of weld beads;
(2) The transition layer should have a high strength (σmin ≥ 6 × 108Pa) and good toughness to prevent the tooth from falling when the saw blade is working;
(3) The sintering performance of the transition layer and the working layer carcass should be similar. Under the same sintering conditions, it has good interfacial bonding strength after sintering (σmin≥6×108Pa);
(4) The thermal expansion coefficients of the transition layer and the working layer should be similar, and the thermal expansion coefficient of the transition layer is slightly smaller to prevent cracks between the transition layer and the working layer during laser welding;
(5) The welding performance of the transition layer and the saw blade base should be as close as possible;
(6) The sintering process has a wide range and is convenient for industrial scale production.
Most of the transition layer formulations are made of single element Co, Ni, two-element FeCo, FeNi, CoNi, FeCu, or FeCoNi, and the transition layer cannot contain low-melting metals, such as tin, because of such elements. It is easy to evaporate and vaporize, and produces pores. Adding a small amount of Mn and Cr to the transition layer material not only can form solid solution strengthening, increase wear resistance, but also effectively reduce welding pores. At present, some foreign companies such as Dr.Fritsch of Germany and Eurotungstone of France have carried out a series of work in the development of transition layer formula and powder preparation. From the aspects of substrate, cutter head, welding strength and surface quality, the transition layer formula has been introduced. Various pre-alloyed powders such as 27-589, V6-790, and NEXT series.
-All diamond tools can be ordered and fabricated!
-Henry Wang | Quote Manager
-WhatsApp:+86-13459035657
-Email: ceo@zdiamondtools.com
-Web www.zdiamondtools.com
Company Profile
Certifications
Company Team
Exhibition
Logistics
FAQ