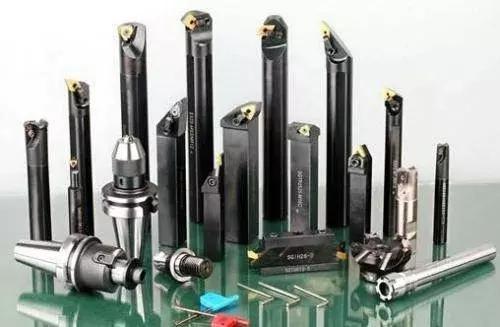
Diamond cutting tool performance
Diamond cutting tools have extremely high performance factors such as hardness and wear resistance, thermal conductivity and low friction. There are many kinds of it, and the manufacturing process is more complicated. The preparation methods of different diamond knives are different, and the application fields are different, and the performance difference is also different. Diamond cutting tools are generally used in the cutting of precious metals such as alloys or gold and the processing of some special parts.
Diamond cutting tool classification
Single crystal diamond cutter single crystal diamond is generally used for cutting large particles (the mass is generally greater than 0.1g, and the minimum diameter is also greater than 3mm). The main reason is that the surface is rough, and the shape and size have very high requirements. Some of the more sophisticated processing applications.
Among them, natural single crystal diamond is the most wearable material in the diamond we just introduced. Its texture is very fine, and then it is finely ground. Its blunt radius of the cutting edge can even be as fine as 0.008-0.005μm. However, the natural single crystal diamond is relatively brittle, and its crystal tends to be opposite to each other. The hardness of crystals in different directions or different crystal planes is different, so we are grinding and using the sharpening. When you should pay attention to choose the right direction to run in.
Synthetic polycrystalline diamond cutting tool Synthetic polycrystalline diamond is a material that combines many diamond crystals into polycrystals at a high temperature through a metal element binder such as cobalt. Although its hardness is not as high as that of single crystal diamond, it is randomly oriented. The polymerization of a kind of diamond crystal grains can be sharply arbitrarily oriented when running in. It is not necessary to use the best cleavage surface as the rake face like natural diamond. When cutting, the cutting edge is very insensitive to sudden accidental damage, so its anti-wear ability is also strong, it can keep the sharpness of the blade for a long time. When processing, we can use very high cutting speed and very The big eat is deep, its service life is generally higher than other materials, and the source of raw materials is also rich. Its price is only one-tenth of that of natural diamond. At present, it has become the high performance of traditional Chinese tools. Alternatives.
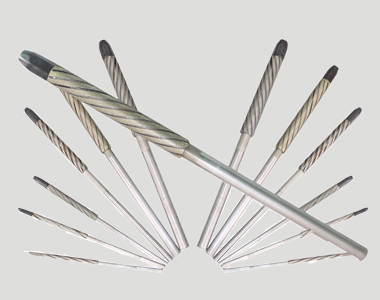
Diamond cutting tool formula
1. Sintered diamond saw blade: specifically, it is divided into cold pressing sintering and hot pressing sintering, and finally pressing sintering.
2. Welded diamond saw blade: divided into high-frequency welding and laser welding. The high-frequency welding welds the cutter head and the base body through a high-temperature melting medium. The laser welding melts the contact edge of the cutter head and the base by a high-temperature laser beam to form a metallurgical bond. .
3. Electroplated diamond saw blade: The cutter head powder is attached to the substrate by electroplating.
-All diamond tools can be ordered and fabricated!
-Henry Wang | Quote Manager
-WhatsApp:+86-13459035657
-Email: ceo@zdiamondtools.com
-Web www.zdiamondtools.com
Company Profile
Certifications
Company Team
Exhibition
Logistics
FAQ