Key words diamond tool|2019-03-07 10:43:51|Technical information|Source Tool manufacturing
Summary Process characteristics of diamond tool grinding The grinding of diamond tools has its own process characteristics. The outstanding features are high hardness of the material, which leads to excessive loss of the grinding wheel during grinding and dimensional instability. Second, the majority of diamond tools For a turning tool or a blade, its...
One. Process characteristics of diamond tool grinding
The grinding of diamond cutters has its own process characteristics. The outstanding features are high hardness of the material, which leads to the loss of the grinding wheel during the grinding process and the dimensional instability. Second, the diamond cutters are mostly turning tools or blades. The position of the grinding point relative to the machine tool is uncertain (such as a change in the thickness of the blade), causing a change in the grinding point. Thirdly, the grinding resistance is large, so that the process system composed of the grinding wheel, the cutter, the fixture and the machine tool produces a relatively large elastic deformation, thereby generating a relatively large "knife" phenomenon.
These three characteristics are the three "roadblockers" for automatic grinding, which directly affect the dimensional accuracy of the tool after molding. If it is not properly solved, it will inevitably lead to poor dimensional accuracy and roughness consistency, low grinding efficiency, and is not suitable for mass production. The use of voice control technology on diamond tool grinding machines can effectively solve these three problems.
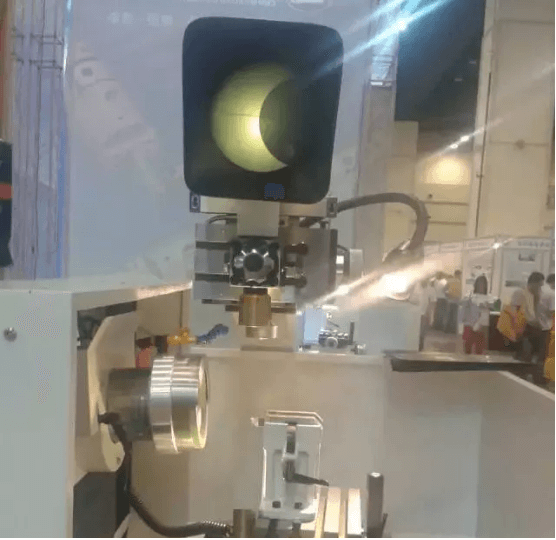
Two. Application of adaptive control technology in rough grinding
The main task of coarse grinding diamond is to improve the grinding efficiency, that is, to set the safety distance as little as possible, and reduce the time of “grinding” the air; remove the grinding allowance as soon as possible within the range of the machine's performance; It was found that the grinding allowance has been removed (the mark is that the grinding resistance is reduced to a minimum).
The friction between the grinding wheel and the diamond tool produces intense sound waves propagating on the process equipment. The monitoring of the sound wave can accurately reflect the grinding condition, such as whether the tool is in contact with the grinding wheel, and whether the pressure between the tool and the grinding wheel (ie the grinding resistance) is eliminated. Wait. If the control system can collect this information in real time and analyze it to adapt the machine control system to it, it is tantamount to installing a sensitive ear on the machine tool, making the machine controller a smarter adaptive system. In fact, the development of the system was also inspired by the sharpening of the workers on site.
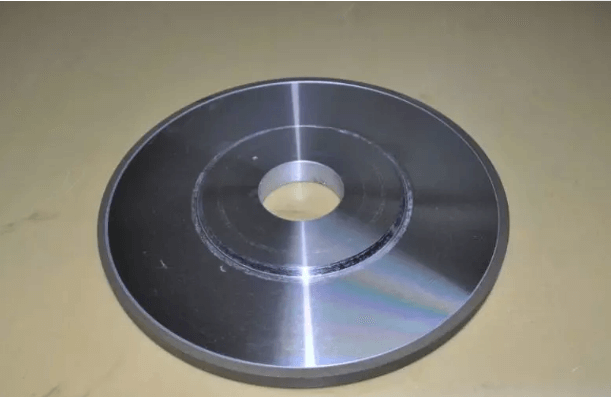
In normal grinding, there are two cases where the acoustic frequency has obvious characteristics. One is the moment when the tool is in contact with the grinding wheel, and the other is when the grinding reaches the final size (the grinding resistance is reduced to a minimum). The former can be used as a fast feed end to start the grinding boundary of the feed; the latter can be used as a sign of grinding completion.
Even in the process of “close contact” between the tool and the grinding wheel, the change of the acoustic frequency can reflect the resistance between the tool and the grinding wheel. This “information” is fed back to the machine controller to adjust the servo feed rate and make the grinding Cutting is done under relatively “constant” resistance, which is of great significance for improving grinding efficiency and extending machine life.
3. The application of "knife grinding method" in fine grinding
The main task of diamond grinding is to accurately and consistently control the final dimensional accuracy of the grinding. The wear of the grinding wheel, the accurate positioning of the sharpening point and the grinding resistance will ultimately affect the machining accuracy. These factors are not related to the movement accuracy of the machine tool, but when the grinding starts (ie, the point of the tool), the end of the grinding, etc. The problem is closely related to the monitoring of the grinding state.
Although the wear amount of the grinding wheel is difficult to measure, and the height of the blade (which affects the position of the grinding point) is difficult to measure within a certain range, the control system with the voice control device can always easily record the exact position of the contact point between the cutting edge and the grinding wheel surface. . Using this as a starting point, the relative feeding can accurately control the dimensional accuracy. This is called “knive grinding method”. Of course, the precondition for the “knife grinding method” is that the previous process has an accurate reference, or it can accurately measure the size before grinding, which can be done with the CCD system online measurement system. In the industry, the manual grinding machine is used to sharpen the knife. The grinding process of the first back angle (also the wiper) of the PCD tool is: grinding the 0.02~0.03mm on the basis of the rough grinding to form 0.05~0.1. Tape of mm. This coincides with the "knife-grinding method".
During the grinding process, the grinding wheel is still continually worn, and the system can detect this wear and compensate in time, compressing the time of “grinding the air” to nearly zero, greatly improving the grinding efficiency.
Sound control technology has a wide range of applications throughout the grinding industry because it solves the common contradictions in grinding. This contradiction is particularly prominent in the grinding of diamonds.
-All diamond tools can be ordered and fabricated!
-Henry Wang | Quote Manager
-WhatsApp:+86-13459035657
-Email: ceo@zdiamondtools.com
-Web www.zdiamondtools.com
Company Profile
Certifications
Company Team
Exhibition
Logistics
FAQ