Key words diamond wire, polycrystalline|2019-05-17 09:27:39|Technical information|Source China Superhard Materials Net
Abstract At present, the technical bottleneck of diamond wire in polycrystalline cutting has been basically solved, and production is rapidly converting into diamond wire cutting. (1) Current status and future trends of diamond wire in polycrystalline industry applications: 1. History: Diamond wire-cut polysilicon wafers face two risks of wire breakage and softening...
At present, the technical bottleneck of diamond wire in polycrystalline cutting has been basically solved, and production is rapidly converting into diamond wire cutting.
(1) Current status and future trends of diamond wire in polycrystalline industry applications:
1. History: Diamond wire-cut polysilicon wafers face two major problems: the risk of disconnection and the difficulty of softening:
(1) Broken wire: Hard spots existing in the ingot crystal may cause wire breakage during the cutting process;
(2) Cashmere: The diamond wire consolidation cutting method results in shallow surface damage and thin surface scratches after cutting, which results in higher reflectivity damage layer, which still exists after the current acid wet method. The higher reflectivity, the efficiency of the battery is nearly 0.4% lower than that of the mortar-cut silicon wafer.
2, the status quo: the combination of diamond wire + black silicon technology can basically solve this problem;
3. Future: Major polysilicon enterprises have begun to promote the promotion of diamond wire + black silicon technology on a large scale. It is expected that the replacement of mortar cutting will be basically completed in 2018. But in any case, driven by the tremendous pressure of technology upgrades and cost reductions in the polysilicon industry, diamond wire-cutting technology has begun to achieve scale applications in the polycrystalline field by superimposing black silicon technology. Considering that the original mortar cutting assets are invested heavily, and the diamond wire transformation cost is low, most polysilicon enterprises may adopt methods to improve the original equipment.
(2) Black silicon texturing technology
In recent years, major polysilicon companies have begun to explore solutions. A more recognized approach is to use black silicon technology in the polysilicon cell segment. The black silicon battery, the core is through the etching technology, on the one hand, on the basis of the conventional silicon wafer surface, the formation of nano-sized small suede surface, thereby increasing the effect of light trapping to reduce the reflectivity and increase the absorption of light; On the other hand, surface recombination is reduced by secondary etching, thereby increasing the absolute value of conversion efficiency of a conventional battery.
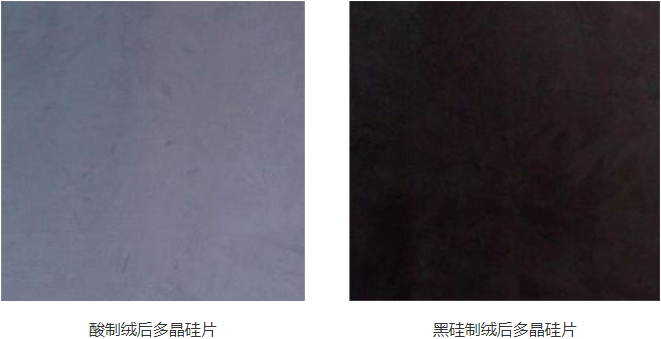
Black silicon cashmere features:
The selectivity of the silicon wafer is not strong; the lower surface reflectance; the appearance of the battery component product is excellent; the difficulty of the battery surface passivation technology is increased; the component CTM loss matching needs to be considered.
Black silicon cashmere implementation:
Reactive ion etching (RIE); financially assisted chemical etching (MACE); graphic mask chemical etching; laser method.
1, dry RIE black silicon

There are three modes of dry black silicon implementation:
(1) RIE mode: physical bombardment > chemical reaction, stroke type pyramidal morphology;
(2) ICP mode: chemical reaction > physical bombardment, the stroke is similar to the inverted pyramid shape;
(3) Purification reaction, no need to damage the process.
2, wet method MACE black silicon
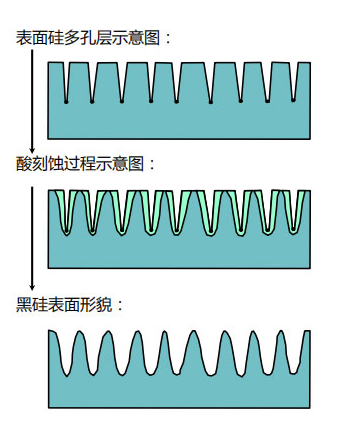
Process: SDE (surface destructive etching) - HF / H202 / AgNO3 (metal porous layer formation) - HF / HNO3 / H2O (acid solution etching) - Surface etching - HF / HCI , SC-2 (metal cleaning removal).
At present, the main factors affecting the mass production of wet process are the removal of metal ions, the stability and repeatability of the texturing process.
(III) Principle of diamond wire cutting polysilicon sheet fluffing additive
The main components of the additive: silicon-based surfactants, organic defoamers, and the like.
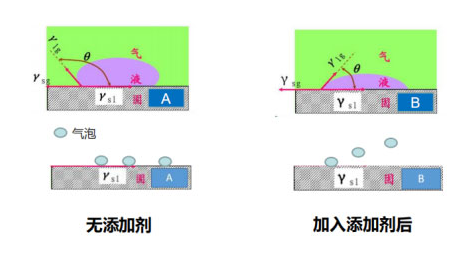
(4) Comparison of technical routes for different diamond wire cutting polysilicon wafers
1, technical performance comparison
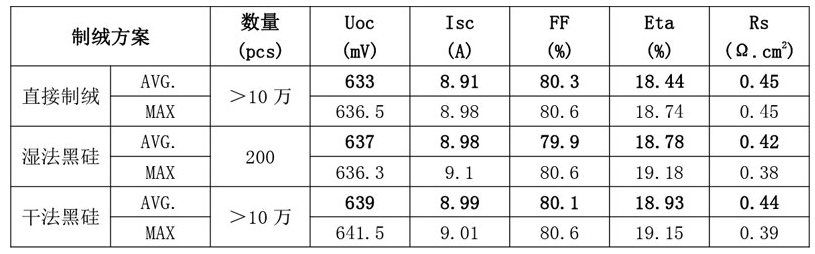
The additive scheme efficiency loss is about 0.1%; the wet black silicon efficiency gain is about 0.25% to 0.4%; and the RIE efficiency gain is about 0.5% to 0.7%.
2. Comparison of QE curve analysis of the cashmere scheme
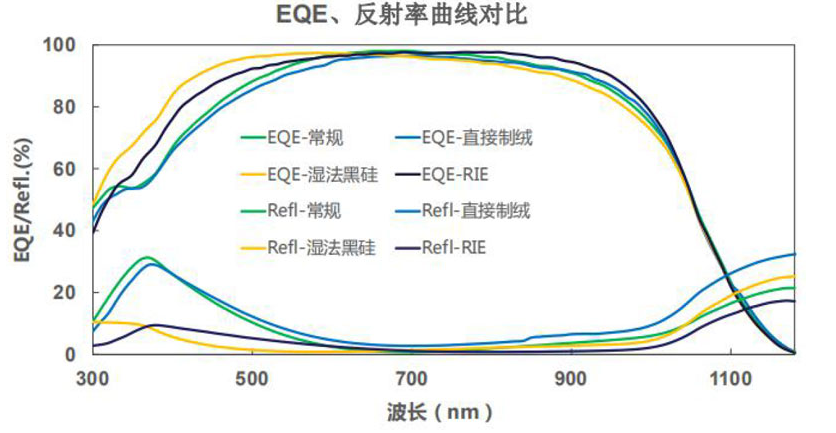
Wet black silicon is best in short-wavelength EQE because of its small suede; dry black silicon has certain improvement in long wave and short wave; direct texturing is similar to conventional mortar cutting polycrystalline conventional acid flocking, long wave reflection The rate is higher than that of conventional mortar acid.
3, battery appearance comparison
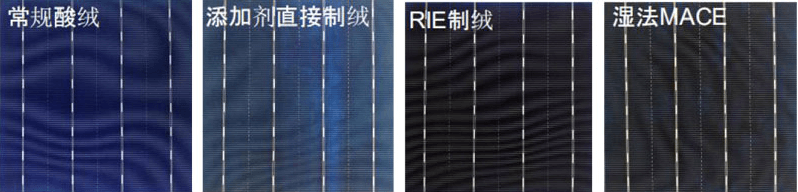
The additive solution has a uniform appearance, a slightly brighter appearance, and a uniform surface; the RIE appearance is black, uniform, and the best performance; the MACE battery has a slightly crystal appearance, and the package is not obvious after packaging.
4. Comparison of industrial application of three schemes

5, component performance comparison
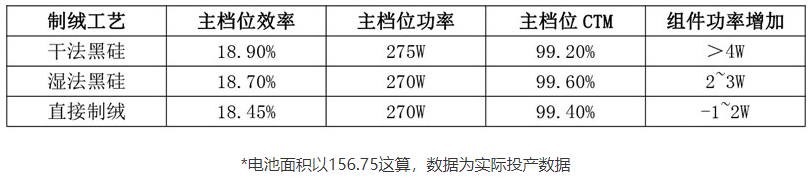
6, component appearance comparison
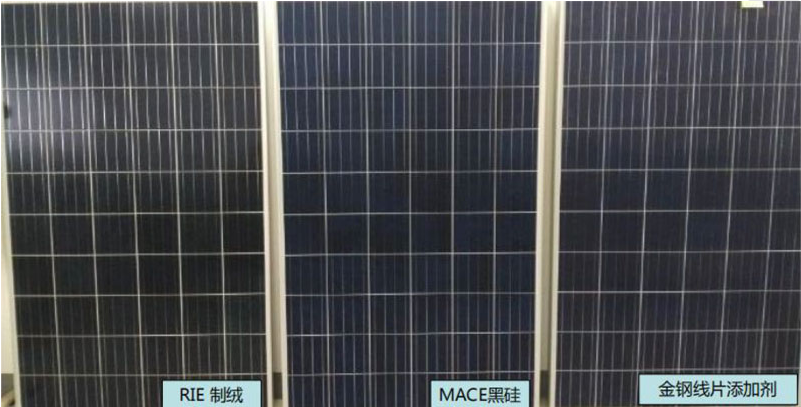
-All diamond tools can be ordered and fabricated!
-Henry Wang | Quote Manager
-WhatsApp:+86-13459035657
-Email: ceo@zdiamondtools.com
-Web www.zdiamondtools.com
Company Profile
Certifications
Company Team
Exhibition
Logistics
FAQ